Custom plastic extrusion adapted to your industry needs
Custom plastic extrusion adapted to your industry needs
Blog Article
Recognizing the Essentials and Applications of Plastic Extrusion in Modern Manufacturing
In the world of contemporary manufacturing, the technique of plastic extrusion plays a crucial duty - plastic extrusion. This complex process, entailing the melting and shaping of plastic through specialized dies, is leveraged throughout various markets for the creation of diverse products. From car components to customer items packaging, the applications are substantial, and the capacity for sustainability is equally outstanding. Unraveling the principles of this procedure reveals the real adaptability and potential of plastic extrusion.
The Basics of Plastic Extrusion Refine
While it may appear complex, the basics of the plastic extrusion procedure are based on relatively straightforward concepts. It is a production procedure in which plastic is thawed and after that shaped right into a constant account with a die. The raw plastic product, often in the kind of pellets, is fed into an extruder. Inside the extruder, the plastic is subjected to heat and stress, causing it to melt. The liquified plastic is after that forced through a designed opening, referred to as a die, to form a long, constant item. The extruded item is cooled and after that reduced to the preferred length. The plastic extrusion procedure is thoroughly utilized in different markets because of its cost-effectiveness, flexibility, and effectiveness.
Different Sorts Of Plastic Extrusion Strategies
Building upon the basic understanding of the plastic extrusion procedure, it is needed to discover the various strategies associated with this manufacturing method. The two primary methods are profile extrusion and sheet extrusion. In profile extrusion, plastic is melted and created right into a continual account, commonly used to create pipelines, poles, rails, and home window frameworks. On the other hand, sheet extrusion creates huge, level sheets of plastic, which are generally additional processed into products such as food packaging, shower curtains, and automobile parts. Each strategy requires specialized machinery and precise control over temperature and stress to make sure the plastic keeps its form during air conditioning. Comprehending these techniques is vital to using plastic extrusion properly in modern-day manufacturing.
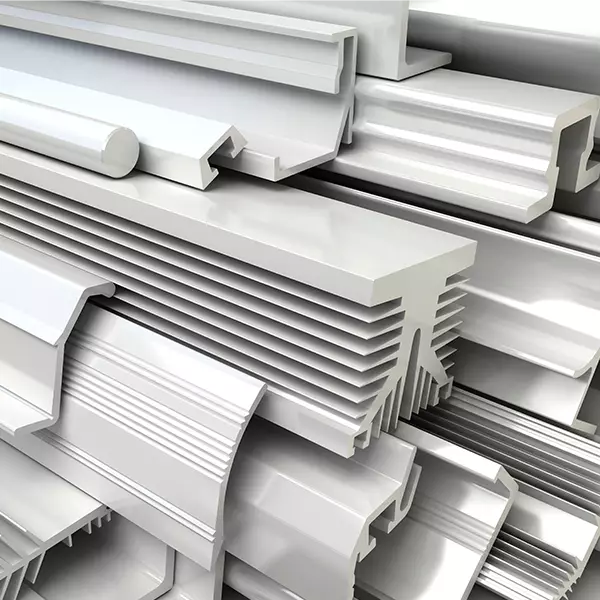
The Duty of Plastic Extrusion in the Automotive Industry
A frustrating majority of parts in contemporary automobiles are products of the plastic extrusion process. This procedure has revolutionized the automobile sector, transforming it right into a much more reliable, cost-effective, and versatile manufacturing market. Plastic extrusion is mainly made use of in the manufacturing of various car parts such as bumpers, grills, door panels, and dashboard trim. The procedure offers an uniform, regular result, making it possible for suppliers to produce high-volume get rid of fantastic precision and marginal waste. The agility of the extruded plastic parts adds to the overall decrease in vehicle weight, boosting gas efficiency. The sturdiness and resistance of these parts to warmth, chilly, and impact boost the durability of vehicles. Thus, plastic extrusion plays an essential role in auto manufacturing.
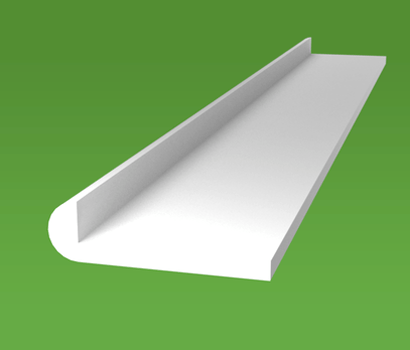
Applications of Plastic Extrusion in Durable Goods Production
Past its substantial influence on the auto industry, plastic dig this extrusion proves equally reliable in the world of customer goods manufacturing. The convenience of plastic extrusion permits producers to make and produce intricate forms and dimensions with high accuracy and performance. The flexibility, flexibility, and cost-effectiveness of plastic that site extrusion make it a preferred option for lots of consumer items suppliers, contributing considerably to the industry's development and advancement.
Ecological Impact and Sustainability in Plastic Extrusion
The pervasive usage of plastic extrusion in manufacturing invites examination of its eco-friendly ramifications. As a procedure that frequently uses non-biodegradable products, the ecological effect can be substantial. Power usage, waste manufacturing, and carbon exhausts are all concerns. Market advancements are increasing sustainability. Effective equipment decreases power usage, while waste monitoring systems recycle scrap plastic, decreasing resources demands. Furthermore, the growth of eco-friendly plastics supplies a more environmentally pleasant alternative. Regardless of these improvements, better innovation is required to mitigate the environmental footprint of plastic extrusion. As society leans in the direction of sustainability, producers should adapt to stay sensible, emphasizing the value of constant research study and improvement in this click to read field.
Verdict
In final thought, plastic extrusion plays a vital function in modern production, especially in the vehicle and consumer items markets. Understanding the basics of this procedure is essential to enhancing its advantages and applications.
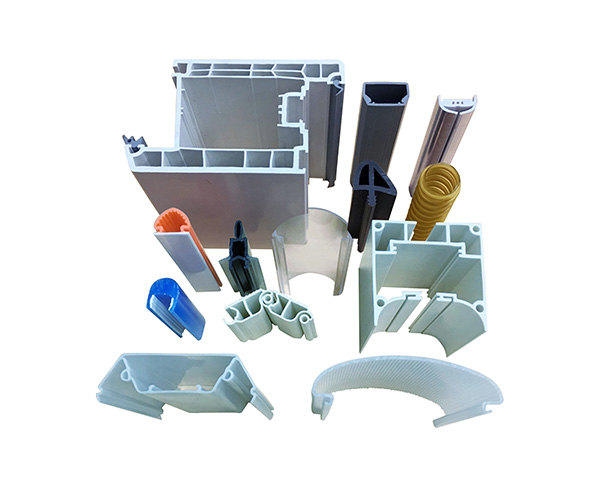
The plastic extrusion process is extensively made use of in different industries due to its efficiency, convenience, and cost-effectiveness.
Building upon the basic understanding of the plastic extrusion procedure, it is essential to check out the different strategies included in this production approach. plastic extrusion. In comparison, sheet extrusion creates big, flat sheets of plastic, which are generally more processed into products such as food product packaging, shower drapes, and automobile components.An overwhelming bulk of parts in modern automobiles are items of the plastic extrusion procedure
Report this page